Understanding Compression Molding Companies: Innovations in Electronics and Medical Supplies
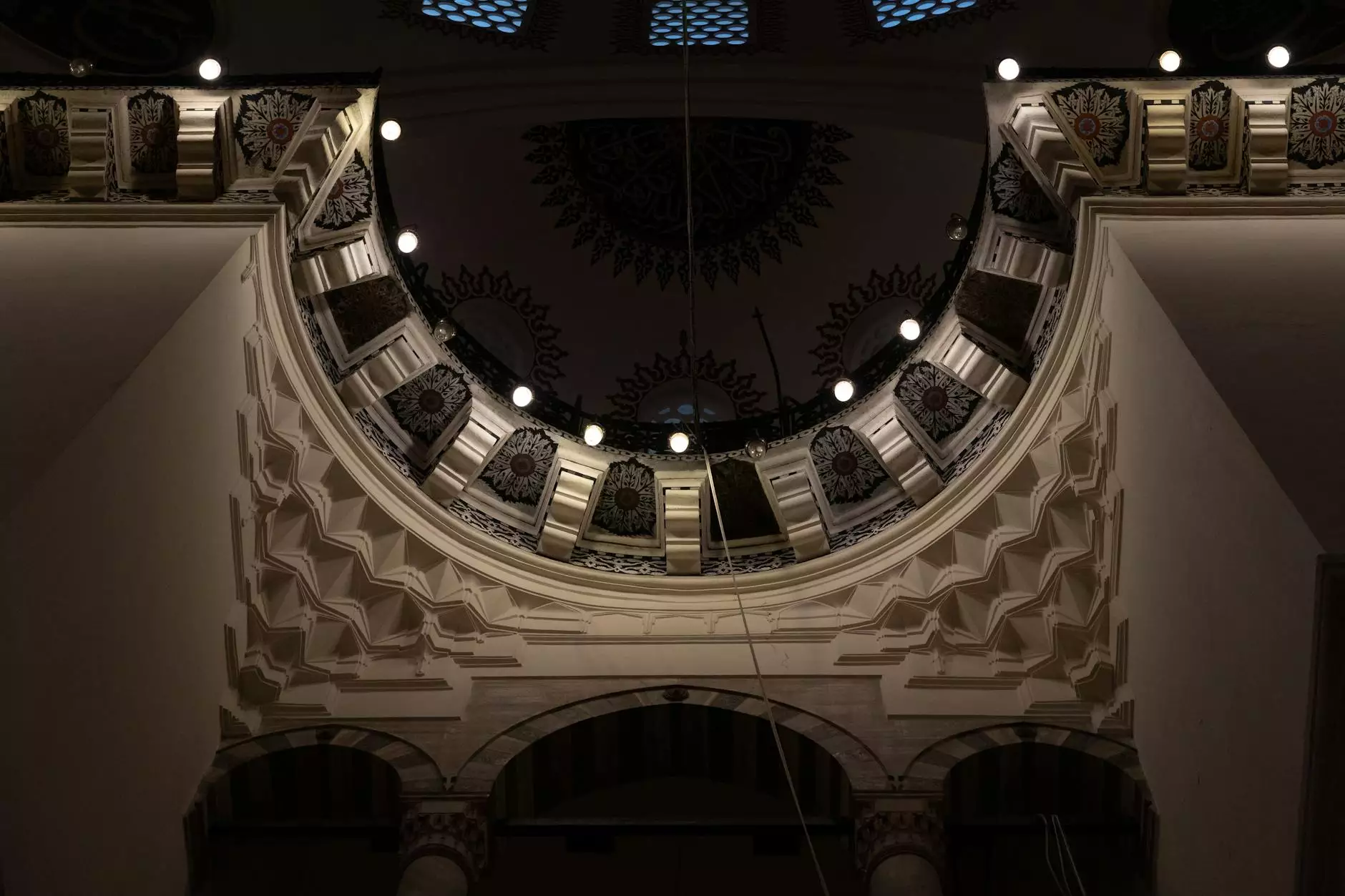
Compression molding has become an essential process in manufacturing, especially for compression molding companies specializing in electronics and medical supplies. This article delves into the significant aspects of this manufacturing method, highlighting its benefits, applications, and the future of the industry, particularly within the context of companies like Nolato.
What is Compression Molding?
Compression molding is a manufacturing process that involves pressing heated plastic or rubber material into a designed mold. The process begins with the introduction of a preheated polymer material into a mold cavity. After that, the mold is closed, and heat and pressure are applied. This method is widely recognized for its efficiency and ability to produce durable parts.
Advantages of Compression Molding
Compression molding offers numerous advantages that make it suitable for various applications:
- Cost-effective Production: This method minimizes waste and reduces material costs, making it ideal for high-volume production.
- Design Flexibility: Compression molding allows for complex shapes and designs, enabling customization in manufacturing.
- Durable Products: The resulting parts are highly resilient and can withstand significant stress and wear, which is critical for medical and electronic applications.
- Reduced Labor Costs: Automation in the compression molding process can lead to lower labor costs and increased productivity.
Applications in Electronics
Compression molding plays a crucial role in the electronics sector, offering reliable and efficient solutions for various components. Some applications include:
- Insulation Components: Molding materials that provide effective insulation properties are essential for electronic devices.
- Connectors and Casing: Precision in molding ensures robust connectors and protective casings for electronic products.
- Keypads and Switches: The production of high-quality keypads that endure constant usage significantly enhances usability in electronic devices.
Applications in Medical Supplies
The medical industry demands high standards for quality and safety. Compression molding companies contribute significantly by manufacturing critical components like:
- Surgical Instruments: Molding processes ensure uniformity and durability necessary for surgical tools.
- Medical Tubing: Precise molding techniques allow for the creation of reliable medical tubing used in various applications.
- Protective Equipment: The production of durable personal protective equipment (PPE) relies heavily on the efficiency of compression molding.
Industry Innovations by Compression Molding Companies
Compression molding companies like Nolato are at the forefront of adopting innovative practices and technologies. Some notable innovations include:
- Eco-friendly Materials: Embracing sustainable practices by utilizing biodegradable materials to reduce environmental impact.
- Smart Manufacturing: Implementing IoT and AI technologies to optimize production processes and enhance quality control.
- Advanced Mold Design: The development of multi-cavity and modular molds streamlines production and improves efficiency.
The Future of Compression Molding in Electronics and Medical Fields
As markets evolve, the demand for advanced manufacturing techniques will continue to rise. The future of compression molding within compression molding companies is promising, with trends such as:
- Increased Automation: Robotics and automated processes will further enhance efficiency, reducing cycle times and costs.
- Customization and Personalization: As demand for personalized products grows, compression molding will adapt to create tailored solutions.
- Adoption of Additive Manufacturing: Integrating 3D printing technology with compression molding could revolutionize design and manufacturing processes, allowing for rapid prototyping and production.
Challenges Faced by Compression Molding Companies
Despite the many advantages, compression molding companies face challenges that need addressing:
- Material Limitations: Some materials may not mold well, requiring continuous research and development.
- Quality Control: Maintaining consistent quality across large production runs can be complex and necessitates stringent quality assurance measures.
- Market Competition: The increasing competition within the industry drives the need for continuous innovation and efficiency improvements.
Conclusion
In conclusion, compression molding companies such as Nolato are pivotal in shaping the future of manufacturing in the electronics and medical supply sectors. The advantages of the compression molding process, from cost efficiency to the ability to produce durable and complex parts, are setting the foundation for ongoing innovation. Embracing new technologies and sustainable practices will ensure these companies remain at the forefront of the industry, delivering high-quality products that meet modern demands.
As we look to the future, it is clear that compression molding will continue to evolve, driving advancements in manufacturing that positively impact various industries. Businesses and manufacturers need to stay informed and adapt to these changes to remain competitive in a rapidly changing market.