CNC Machining Parts: Revolutionizing the Manufacturing Industry
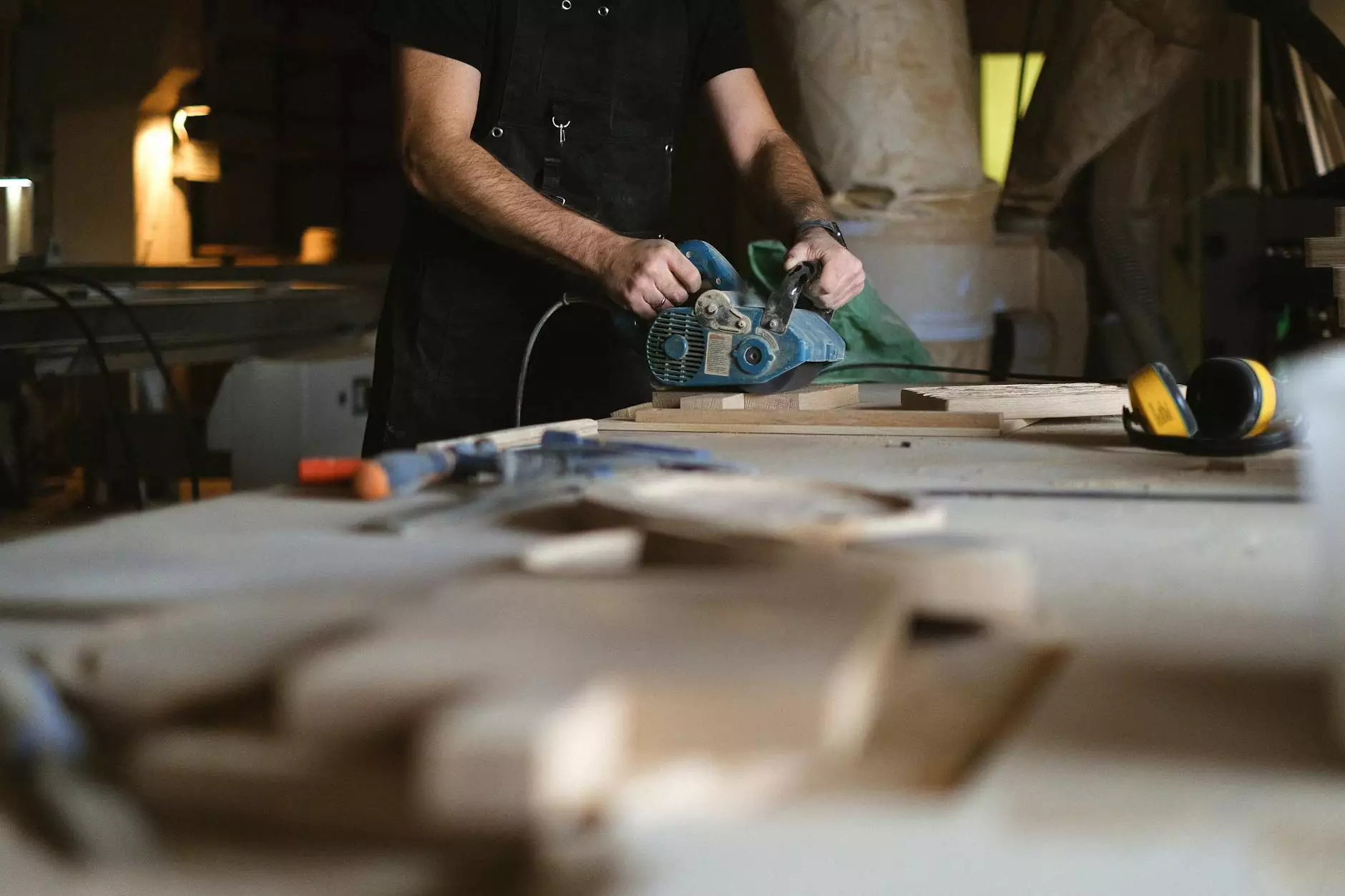
CNC machining has transformed the landscape of the manufacturing industry, particularly through its high-precision and efficiency in producing CNC machining parts. These components are integral for various sectors, including automotive, aerospace, medical, and electronics. In this comprehensive article, we will delve into the intricacies of CNC machining parts, exploring their types, applications, advantages, and how they are positively impacting businesses across the globe.
Understanding CNC Machining
CNC, which stands for Computer Numerical Control, refers to a method of automating the control of machine tools through computers. Unlike traditional machining, where human operators direct the machines manually, CNC machines use pre-programmed software to dictate the movements of production equipment. This ensures a high level of accuracy and repetition that manual processes cannot achieve.
How CNC Machining Works
The process begins with a 3D design created using Computer-Aided Design (CAD) software. This design is then translated into a machine-readable code through Computer-Aided Manufacturing (CAM) software. The CNC machine follows this code to perform operations such as milling, turning, and grinding with remarkable precision.
The Importance of CNC Machining Parts
CNC machining parts are vital for the effective functioning of various machinery and equipment. Their significance can be observed through several critical factors:
1. Precision and Accuracy
The primary advantage of CNC machining parts is their incredible precision. CNC machines can manufacture components to tolerances of ±0.001 inches or better, which is crucial in industries where minute tolerances can significantly impact performance and safety.
2. Complex Geometries
CNC technology allows for the production of parts with intricate designs that would be impossible to achieve with traditional machining methods. This capability opens doors to creativity and innovation in product design.
3. Consistency and Repeatability
Once a CNC program is established, it can produce identical parts consistently without variation. This repeatability is invaluable for bulk production, ensuring that every piece meets the required specifications.
4. Reduced Labor Costs
By automating the machining process, businesses can minimize labor costs and reduce the likelihood of human error. Technicians can oversee multiple machines simultaneously, further enhancing operational efficiency.
Applications of CNC Machining Parts
The versatility of CNC machining parts means they are employed in a wide range of applications, including:
- Aerospace Industry: Components for aircraft and spacecraft require utmost precision due to safety concerns. CNC machining produces lightweight, high-strength parts that meet stringent standards.
- Automotive Sector: From engine blocks to custom parts, CNC machining enables car manufacturers to produce reliable and optimal components swiftly.
- Medical Devices: Components used in medical instruments require high levels of accuracy and cleanliness. CNC machines can create elements like surgical tools and implants with precision.
- Electronics Manufacturing: CNC machining is essential for producing circuit boards and enclosures that hold delicate electronic components.
Types of CNC Machining Parts
There are various types of CNC machining parts, each serving a specific purpose. Some of the notable ones include:
1. CNC Milled Parts
CNC milling involves the removal of material from a solid block to create desired shapes. The result is highly detailed and precise parts that can be tailored for a variety of applications.
2. CNC Turned Parts
Turning is the process of rotating the material on a lathe and removing material using cutting tools. CNC turned parts are cylindrical and are commonly used in the automotive and aerospace industries.
3. CNC Cut Parts
This involves using CNC cutters to slice through various materials. Types of cutting can include laser cutting, water jet cutting, or plasma cutting, ideal for producing flat parts.
Benefits of Using CNC Machining Parts
Incorporating CNC machining parts in production brings numerous advantages:
- Increased Efficiency: CNC machines operate faster and more efficiently than traditional methods.
- Improved Safety: Automation reduces the risk of injury associated with manual machining.
- Cost-Effectiveness: Despite initial setup costs, the long-term savings due to reduced labor and material waste make CNC machining a financially sound choice.
- Flexibility: Changing designs or products is relatively easy and can be achieved by simply altering the software.
CNC Machining Parts and Sustainability
As industries worldwide strive for sustainability, CNC machining also plays a role. The precision of CNC machining leads to less waste generation, as materials are utilized more effectively. Additionally, advancements in machining technologies allow for the use of eco-friendly materials.
Choosing the Right CNC Machining Parts Supplier
Selecting the right supplier for CNC machining parts is crucial for ensuring quality and reliability. Here are several factors to consider:
- Experience and Expertise: Look for suppliers with a proven track record and a deep understanding of CNC technology.
- Quality Control Processes: Ensure the supplier has stringent quality control measures to guarantee the parts meet specifications.
- Certifications: Check for industry certifications like ISO, which indicate a commitment to quality standards.
- Customer Support: Choose suppliers who provide excellent customer service and support throughout the order process.
The Future of CNC Machining Parts
The future of CNC machining parts is bright, with continuous advancements in technology leading to new possibilities. Innovations such as 3D printing integration, smart machining, and enhanced software capabilities are paving the way for even greater efficiency and creativity in manufacturing.
1. Integration with IoT
The Internet of Things (IoT) is redefining how machines communicate within manufacturing environments. As CNC machines become smarter, they will facilitate real-time monitoring and predictive maintenance, ensuring uninterrupted production.
2. Advances in Materials
New materials with unique properties are emerging, allowing engineers to design parts that are stronger, lighter, and more adaptable to changing environments.
Conclusion
In conclusion, CNC machining parts are at the forefront of the modern manufacturing industry, proving essential across multiple sectors. The combination of precision, efficiency, and flexibility equates to a significant competitive advantage for businesses. By understanding the importance and benefits of CNC machining parts, companies can harness this technology to improve their production processes, reduce costs, and drive innovation. As we look to the future, the evolution of CNC technology promises to open new avenues for exploration and growth, solidifying its status as a cornerstone of advanced manufacturing.
For businesses looking to elevate their operations, choosing a reliable partner like DeepMould can provide access to top-notch CNC machining parts tailored to meet specific demands in the metal fabrication industry. Embrace the revolution in manufacturing and stay ahead with CNC machining parts.